After more than 32 years of supplying the hot water that maintains River Journey’s environmental systems, the building’s original boilers are being replaced with modern upgrades.
Since before opening its doors to the public in 1992, River Journey has used gas-fired boiler banks to heat water that is piped throughout the entire building. Along the way, the hot water passes through heat exchangers, which use that energy to warm the water in the building’s exhibits and to warm the air in galleries and behind-the-scenes areas via the HVAC system.
“Nobody thinks about boilers but me and Manager of Life Support Systems and HVAC Sean Hill and a few others until they’re broken and you’re cold,” says Aquarium Director of Facilities and Safety Rodney Fuller. “But they impact you every day.”
The replacement involves removing the old boilers and the piping and ventilation systems that connect to them in the fifth-floor boiler room. Then, the new system will be installed, and new pipes and ductwork will be fitted to accommodate the upgraded hardware.
The original boilers’ longevity is a testament to the quality of their engineering and manufacturing, not to mention the facilities and operations teams’ herculean effort in maintaining them for more than 30 years.
Each bank of the old system consisted of six cast iron chambers fired by natural gas. The new boilers are also cast iron, but boiler designs have significantly improved over the last thirty years.
“The technology is very different,” Fuller says. “We’ve gone with something a lot more energy efficient.”
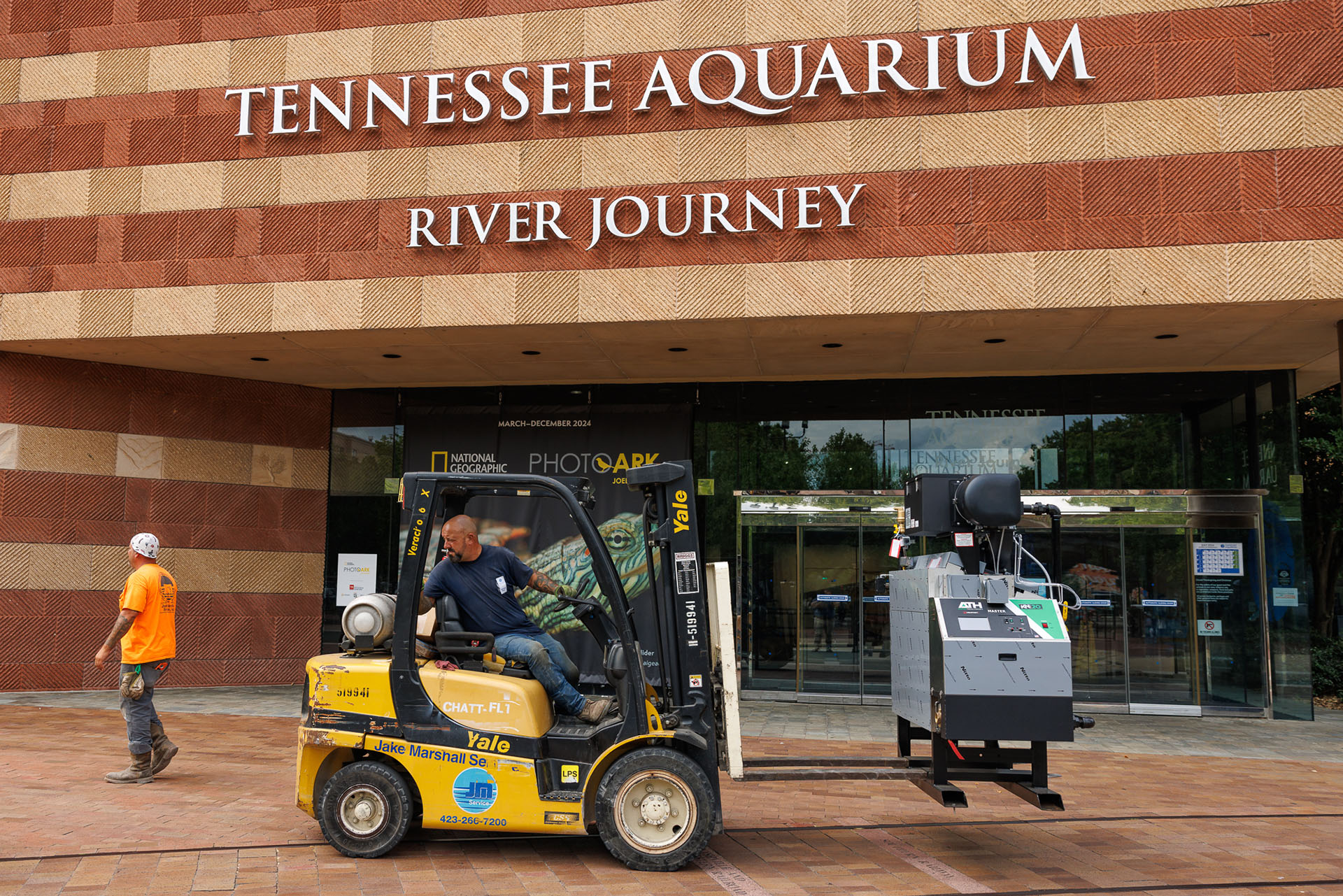
New boiler equipment is moved across the Aquarium Plaza.
The building’s replacement boilers are qualified by the Leadership in Energy and Environmental Design (LEED) and operate more environmentally friendly and economically than the original units. While their replacement is a significant capital expense, the cost was offset by a $75,000 grant from sustainability nonprofit Southface’s GoodUse.
GoodUse provides technical assistance and funding in the form of matching grants to nonprofits to assist them with resource efficiency upgrades to their facilities. These upgrades save the nonprofit valuable funds on utility bills that can be reallocated into their mission. Information about GoodUse can be found here.
This program helps nonprofits reduce utility costs so that those funds can be used for mission-focused efforts. According to Southface’s estimates, the new boilers will save the Aquarium approximately $30,000 annually.
To avoid significant service interruptions, the Aquarium’s facilities team carefully prepared and selected contractors for this operation to ensure the process proceeded swiftly and without incident or complication.
A boiler replacement at the Tennessee Aquarium is also a high-profile event for boiler manufacturer Advanced Thermal Hydronics (ATH), which had representatives directly involved in the replacement to ensure the installation was successful.